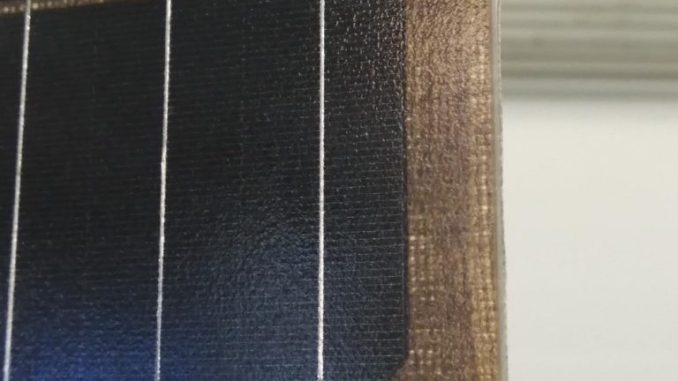
Francouzský institut solární energie INES vyvinul nové fotovoltaické moduly s termoplasty a přírodními vlákny pocházejícími z Evropy, jako je len a čedič. Cílem vědců je snížit ekologickou stopu a hmotnost solárních panelů a zároveň zlepšit recyklaci.
Výzkumníci z francouzského Národního institutu pro sluneční energii (INES) – divize Francouzské komise pro alternativní energie a atomovou energii (CEA) – vyvíjejí solární moduly s novými biologickými materiály na přední a zadní straně.
„Protože se uhlíková stopa a analýza životního cyklu nyní staly základními kritérii při výběru fotovoltaických panelů. A v příštích několika letech se v Evropě stane klíčovým prvkem získávání materiálů,“ řekl Anis Fouini, ředitel CEA-INES.
Aude Derrier, koordinátorka výzkumného projektu, uvedla, že její kolegové se podívali na různé materiály, které již existují, aby našli takový, který by výrobcům modulů umožnil vyrábět panely. Ty zlepšují výkon, odolnost a náklady a zároveň snižují dopad na životní prostředí. První demonstrátor se skládá z heterojunkčních (HTJ) solárních článků integrovaných do celokompozitního materiálu.
,,Přední strana se vyrábí z polymeru plněného skelnými vlákny, který poskytuje průhlednost,“ řekl Derrier. „Zadní strana se vyrábí z kompozitu na bázi termoplastů, do kterého se integruje tkaní dvou vláken, lnu a čediče, což zajistí mechanickou pevnost, ale také lepší odolnost proti vlhkosti.“
Solární panely a jejich recyklace
Len pochází ze severní Francie, kde se již nachází celý průmyslový ekosystém. Čedič se získává jinde v Evropě a je tkaný průmyslovým partnerem INES. To snížilo uhlíkovou stopu o 75 gramů CO2 na watt ve srovnání s referenčním modulem o stejném výkonu. Optimalizovala se i hmotnost, která činí méně než 5 kilogramů na metr čtvereční.
„Tento modul se zaměřuje na střešní fotovoltaiku a integraci budov,“ řekl Derrier. „Výhodou je, že má přirozeně černou barvu, bez potřeby zadního listu. Z hlediska recyklace je díky termoplastům, které lze přetavit, separace vrstev i technicky jednodušší.“
Modul lze vyrobit bez přizpůsobení aktuálních procesů. Derrier řekl, že myšlenka se dá předat technologii výrobcům bez dalších investic.
„Jedinou nezbytností se zdá mít mrazáky na uskladnění materiálu. A nezačínat proces síťování pryskyřice, ale většina výrobců dnes používá prepreg a zdají se na to již vybaveni,“ řekla.
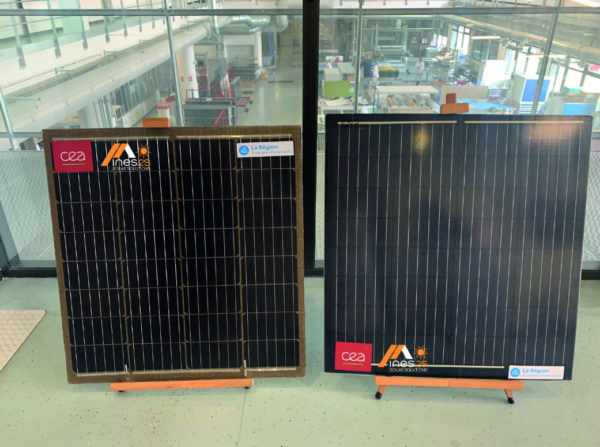
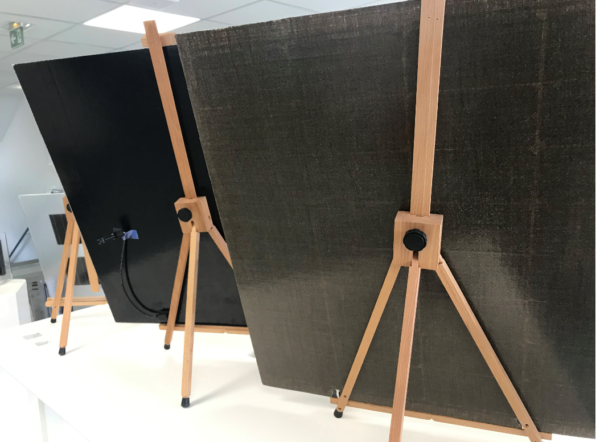
Vědci INES se také zabývali problémy s dodávkami solárního skla, s nimiž se setkávají všichni fotovoltaičtí hráči, a pracovali na opětovném použití tvrzeného skla.
„Pracovali jsme na druhém životě skla a vyvinuli jsme modul vyrobený z opětovně použitého 2,8 mm skla, které pochází ze starého modulu,“ řekl Derrier. ,,Také jsme použili termoplastickou zapouzdřovací látku, která nevyžaduje zesítění, a proto bude snadno recyklovatelná, a termoplastický kompozit s lněným vláknem pro odolnost.“
Bezčedičové zadní čelo modulu má přírodní lněnou barvu. Což by mohlo být pro architekty esteticky zajímavé například z hlediska začlenění fasády. Navíc výpočetní nástroj INES ukázal 10% snížení uhlíkové stopy.
Fotovoltaické řetězce
,,Nyní se zdá nutné zpochybnit fotovoltaické dodavatelské řetězce,“ řekl Jouini. „S pomocí regionu Rhône-Alpes v rámci Mezinárodního plánu rozvoje jsme se proto vydali hledat hráče mimo solární sektor. Abychom našli nové termoplasty a nová vlákna. Mysleli jsme také na současný proces laminace, který je velmi energeticky náročný.“
Mezi natlakováním, lisováním a ochlazovací fází trvá laminování obvykle 30 až 35 minut při provozní teplotě kolem 150°C až 160°C.
,,Ale u modulů, které stále více obsahují materiály navržené v ekologickém designu, se zdá nutné přeměnit termoplasty při teplotě kolem 200°C až 250°C, s vědomím, že technologie HTJ se jeví citlivá na teplo a nesmí překročit 200°C,“ řekl Derrier.
Výzkumný ústav se spojil s francouzským specialistou na indukční termokompresi Roctool. Proto aby zkrátil doby cyklu a vytvořil tvary podle potřeb zákazníků. Společně vyvinuli modul se zadním čelem z termoplastického kompozitu polypropylenového typu, do kterého se integrovala recyklovaná uhlíková vlákna. Přední strana se vyrábí z termoplastu a sklolaminátu.
,,Indukční termokompresní proces společnosti Roctool umožňuje rychle zahřát dvě přední a zadní desky. Aniž by bylo nutné dosáhnout 200°C v jádru článků HTJ,“ řekl Derrier.
Společnost tvrdí, že investice se jeví nižší a proces může dosáhnout doby cyklu jen několik minut při spotřebě méně energie. Technologie se zaměřuje na výrobce kompozitů, aby jim umožnila vyrábět díly různých tvarů a velikostí. A zároveň integrovat lehčí a odolnější materiály.
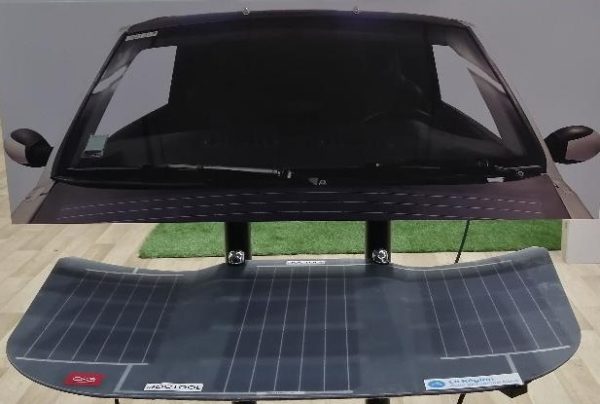
Zdroj: pv-magazine, Vapol